Thư viện tri thức trực tuyến
Kho tài liệu với 50,000+ tài liệu học thuật
© 2023 Siêu thị PDF - Kho tài liệu học thuật hàng đầu Việt Nam
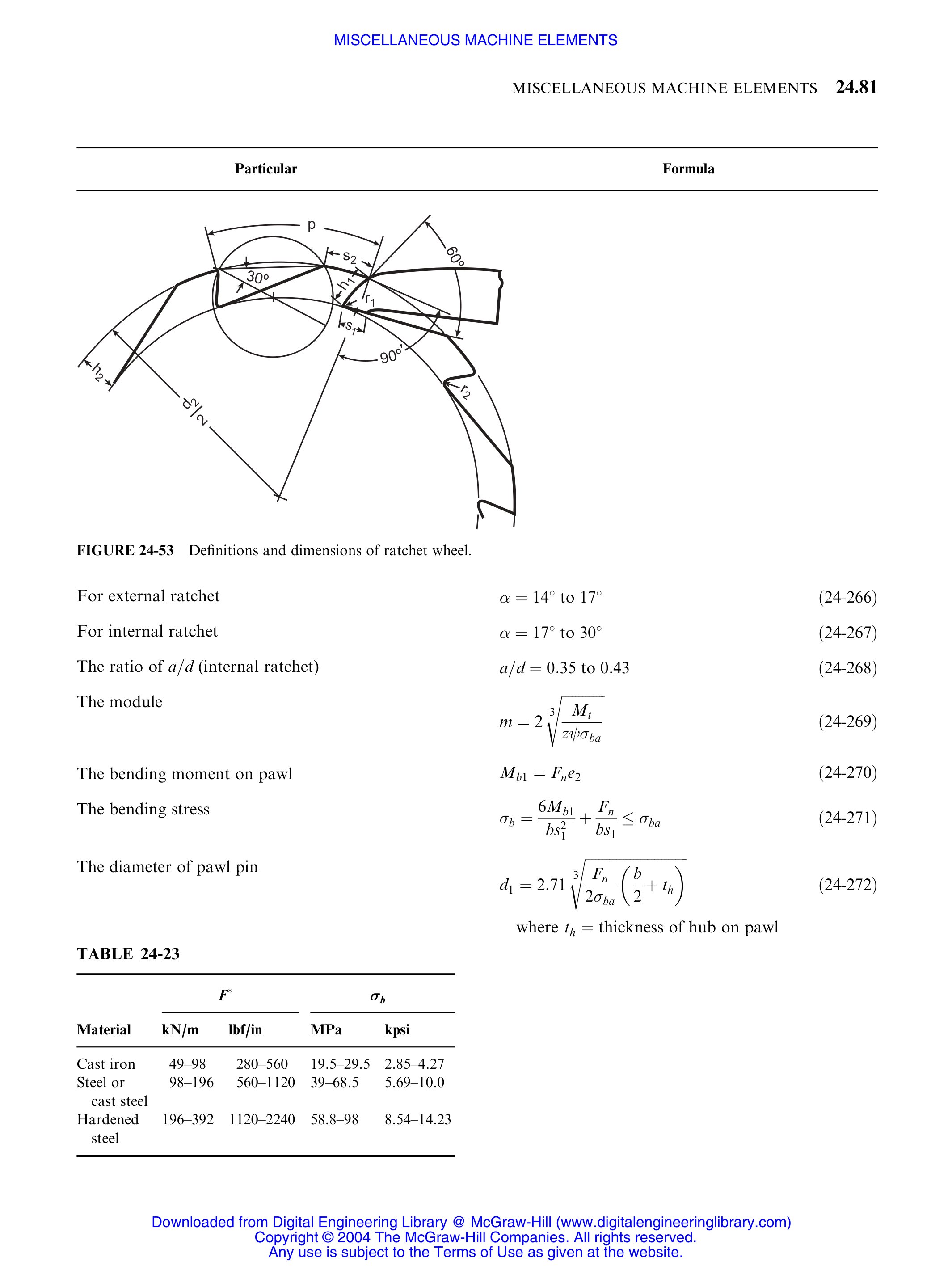
Machine Design Databook Episode 3 part 7 potx
Nội dung xem thử
Mô tả chi tiết
For external ratchet
For internal ratchet
The ratio of a=d (internal ratchet)
The module
The bending moment on pawl
The bending stress
The diameter of pawl pin
¼ 148 to 178 ð24-266Þ
¼ 178 to 308 ð24-267Þ
a=d ¼ 0:35 to 0:43 ð24-268Þ
m ¼ 2 3
ffiffiffiffiffiffiffiffiffiffiffiffi
Mt
z ba s
ð24-269Þ
Mb1 ¼ Fne2 ð24-270Þ
b ¼ 6Mb1
bs2
1
þ
Fn
bs1
ba ð24-271Þ
d1 ¼ 2:71 3
ffiffiffiffiffiffiffiffiffiffiffiffiffiffiffiffiffiffiffiffiffiffiffiffiffiffiffiffiffi
Fn
2ba b
2 þ th
s
ð24-272Þ
where th ¼ thickness of hub on pawl
Particular Formula
p
s2
s1
r1
r2
h1
d2
2
h2
FIGURE 24-53 Definitions and dimensions of ratchet wheel.
TABLE 24-23
F b
Material kN/m lbf/in MPa kpsi
Cast iron 49–98 280–560 19.5–29.5 2.85–4.27
Steel or
cast steel
98–196 560–1120 39–68.5 5.69–10.0
Hardened
steel
196–392 1120–2240 58.8–98 8.54–14.23
MISCELLANEOUS MACHINE ELEMENTS 24.81
Downloaded from Digital Engineering Library @ McGraw-Hill (www.digitalengineeringlibrary.com)
Copyright © 2004 The McGraw-Hill Companies. All rights reserved.
Any use is subject to the Terms of Use as given at the website.
MISCELLANEOUS MACHINE ELEMENTS
24.9 GENEVA MECHANISM
SYMBOLS2,3
a ¼ r1
sin center distance, m (in)
F1 the component of force acting on the crank or the driving shaft
due to the torque, M1t, kN (lbf ) (Fig. 24-57)
F2 the component of force acting on the driven Geneva wheel shaft
due to the torque M2t, kN (lbf ) (Fig. 24-57)
F2ðmaxÞ maximum force (pressure) at the point of contact between the
roller pin and slotted Geneva wheel, kN (lbf )
FðmaxÞ the component of maximum friction force at the point of
contact due to the friction torque M2t, on the driven Geneva
wheel shaft, kN (lbf )
FiðmaxÞ the component of maximum inertia force at the point of contact
due to the inertia torque on the driven Geneva wheel shaft,
kN (lbf )
i ¼ z 2
z gear ratio
J polar moment of inertia of all the masses of parts attached to
Geneva wheel shaft, m4 (in4
)
k the working time coefficient of the Geneva wheel
M1t total torque on the driver or crank, N m (lbf in)
M2t total torque on the driven or Geneva wheel, N m (lbf in)
M2ti inertia torque on the Geneva wheel, N m (lbf in)
M2t friction or resistance torque on Geneva wheel, N m (lbf in)
n0 speed, rps
n speed, rpm
P power, kW (hp)
r1 radius to center of driving pin, m (in)
r2 radius of Geneva wheel, m (in)
r
0
2 distance of center of semicircular end of slot from the center of
Geneva wheel, m (in)
ra2 outside radius of Geneva wheel, which includes correction for
finite pin diameter, m (in)
rp pin radius, m (in)
Rr ¼ r2
r1
radius ratio
t total time required for a full revolution of the driver or crank, s
ti time required for indexing Geneva wheel, s
tr time during which Geneva wheel is at rest, s
v velocity, m/s
z number of slots on the Geneva wheel
crank angle or angle of driver at any instant, deg (Fig. 24-54)
2a angular acceleration, m/s2 (ft/s2
)
angular acceleration of Geneva wheel, m/s2 (ft/s2
)
m angular position of the crank or driver radius at which the
product ! 2a is maximum, deg
angle of the driven wheel or Geneva wheel at any instant, deg
(Fig. 24-54)
¼ r1
a the ratio of the driver radius to center distance
efficiency of Geneva mechanism
24.82 CHAPTER TWENTY-FOUR
Downloaded from Digital Engineering Library @ McGraw-Hill (www.digitalengineeringlibrary.com)
Copyright © 2004 The McGraw-Hill Companies. All rights reserved.
Any use is subject to the Terms of Use as given at the website.
MISCELLANEOUS MACHINE ELEMENTS
locking angle of driver or crank, rad or deg
ratio of time of motion of Geneva wheel to time for one
revolution of driver or crank
¼ 360
2z semi-indexing or Geneva wheel angle, or half the angle
subtended by an adjacent slot, deg (Fig. 24-54)
crank or driver angle, deg (Fig. 24-54)
! ¼ 2n
60 angular velocity of driver or crank (assumed constant), rad/s
!1, !2 angular velocities of driver or crank and Geneva wheel,
respectively, rad/s
a1 β
α
φ
ψ
a2
a3
ω2
r2
r1
ω1
a
FIGURE 24-54 Design of Geneva mechanism.
The angular velocity (constant) of driver or crank
Gear ratio
The semi-indexing angle or Geneva wheel angle or
half the angle subtended by two adjacent slots
The angle through which the Geneva wheel rotates
EXTERNAL GENEVA WHEEL
The angle of rotation of driver through which the
Geneva wheel is at rest or angle of locking action
(Fig. 24-55)
The crank or driver angle
!1 ¼ 2n
60 ð24-273Þ
i ¼ angle moved by crank or driver during rotation
angle moved by Geneva wheel during rotation
i ¼ z 2
z ð24-274Þ
¼ 360
2z or
z ð24-275Þ
2 ¼ 360
z or 2
z ð24-276Þ
¼ 2ð Þ ¼ þ 2 ¼
z
ðz þ 2Þ ð24-277Þ
¼
2 ¼ ðz 2Þ
2z ð24-278Þ
Particular Formula
MISCELLANEOUS MACHINE ELEMENTS 24.83
Downloaded from Digital Engineering Library @ McGraw-Hill (www.digitalengineeringlibrary.com)
Copyright © 2004 The McGraw-Hill Companies. All rights reserved.
Any use is subject to the Terms of Use as given at the website.
MISCELLANEOUS MACHINE ELEMENTS
DISPLACEMENT
The center distance (Fig. 24-55)
The radius ratio
The ratio of crank radius to center distance
The relation between crank angle and Geneva wheel
angle
VELOCITY
The angular velocity of the Geneva wheel
The maximum angular velocity of Geneva wheel at
angle ¼ 0
a ¼ r1
sin ð24-279Þ
Rr ¼ r2
r1
¼ cot ð24-280Þ
¼ r1
a ¼ sin ¼ sin
z ð24-281Þ
¼ tan1
sin
1 cos
ð24-282Þ
!2 ¼ d
dt ¼ ðcos Þ
1 2 cos þ 2 !1 ð24-283aÞ
!2 ¼ sinð=zÞðcos sin =zÞ
1 2 sinð=zÞ cos þ sin2 =z
!1 ð24-283bÞ
!2ðmaxÞ ¼
d
dt
max
¼
1 !1
¼
sin
z
1 sin
z
!1 ð24-283cÞ
Particular Formula
ro2
r1
90”
r’2
a
ω1
ω2
ψ
φ
FIGURE 24-55 External Geneva mechanism.
24.84 CHAPTER TWENTY-FOUR
Downloaded from Digital Engineering Library @ McGraw-Hill (www.digitalengineeringlibrary.com)
Copyright © 2004 The McGraw-Hill Companies. All rights reserved.
Any use is subject to the Terms of Use as given at the website.
MISCELLANEOUS MACHINE ELEMENTS