Thư viện tri thức trực tuyến
Kho tài liệu với 50,000+ tài liệu học thuật
© 2023 Siêu thị PDF - Kho tài liệu học thuật hàng đầu Việt Nam
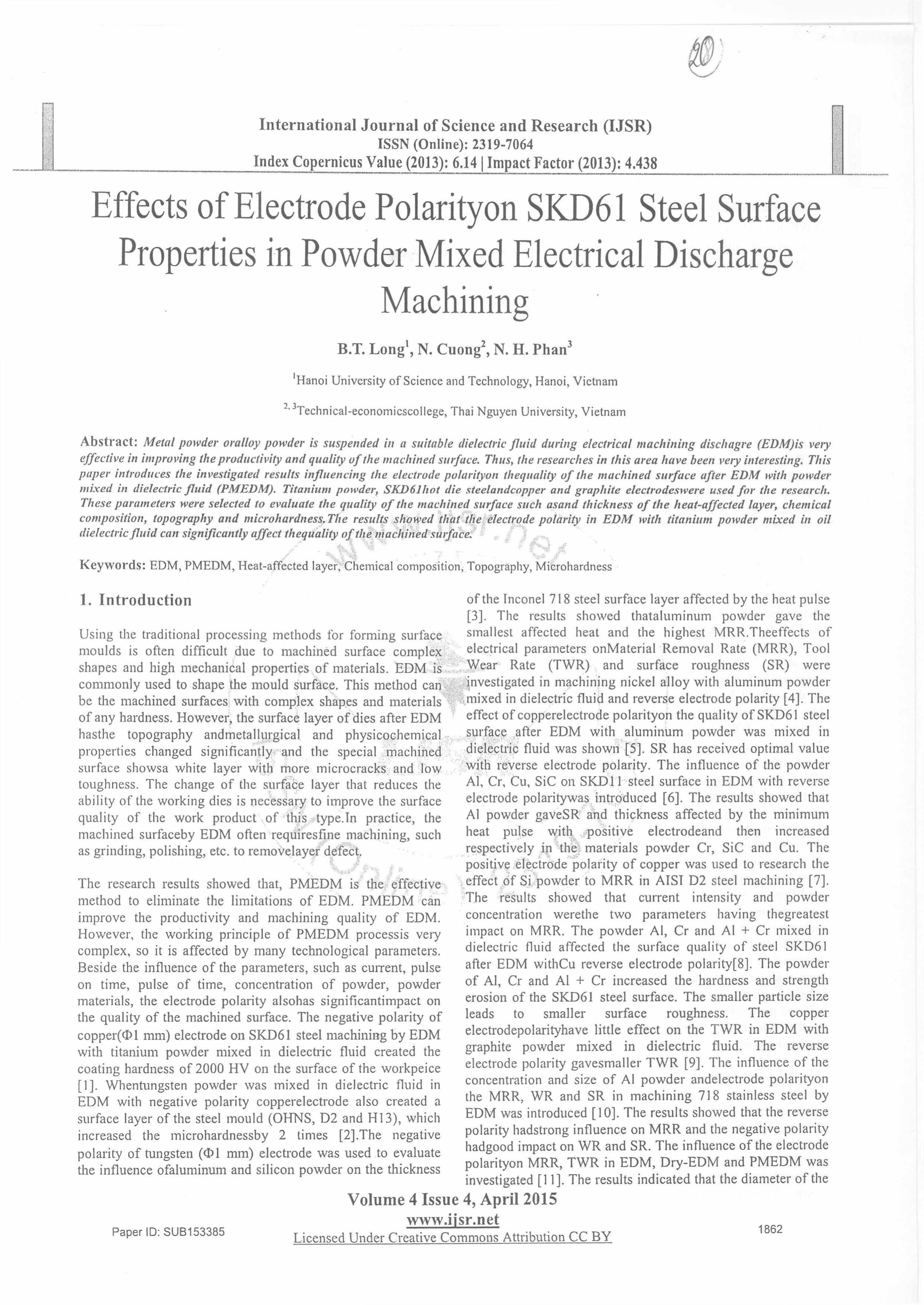
Effects of Electrode Polarity on SKD61 Steel Surface Properties in Powder Mixed Electrical Discharge Machining
Nội dung xem thử
Mô tả chi tiết
I n t e r n a t io n a l J o u r n a l o f S c ie n c e a n d R e s e a r c h (I J S R )
ISSN (Online): 2319-7064
Index Copernicus V alue (2013): 6.14 I Im pact Factor (2013): 4.438
Ị..
Effects of Electrode Polarity on SKD61 Steel Surface
Properties in Powder Mixed Electrical Discharge
Machining
B.T. Long', N. Cuong2, N. H. Phan3
'H a n o i U n iv e r s ity o f S c ie n c e and T e c h n o lo g y , H a n o i, V ie tn a m
2' 3T e c h n ic a l-e c o n o m ic sc o l!e g e , T h ai N g u y e n U n iv e r sity , V ie tn a m
Abstract: MetaI powder oralloy powder is suspended in a suitable dielectric fluid during electrical machining dischagre (EDM)is veiy
effective in improving the productivity anti quality o f the machined surface. Thus, the researches in this area have been very interesting. This
paper introduces the investigated results influencing the electrode polarityon theqnality o f the machined surface after EDM with powder
mixed in dielectric flu id (PMEDM). Titanium powder, SKD61hot die steelandcopper and graphite electrodeswere used fo r the research.
These parameters were selected to evaluate the quality o f the machined surface such asand thickness o f the heat-affected layer, chemical
composition, topography and microhardness.The results showed that the electrode polarity in EDM with titanium powder mixed in oil
dielectric fluid can significantly affect th equality o f the machined surface.
K eyw ords: E D M , P M E D M , H e a t-a ffe c te d la y er. C h e m ica l c o m p o s itio n , T o p o g ra p h y , M icro h a rd n ess
1. Introduction
Using the traditional processing methods for forming surface
moulds is often difficult due to machined surface complex
shapes and high mechanical properties o f materials. EDM -is
comm only used to shape the m ould surface. This method can
be the machined surfaces; w ith complex shapes and materials
o f any hardness. However, the surface layer o f dies after EDM
hasthe topography andmetallurgical and physicochemical
of the Inconel 718 steel surface layer affected by the heat pulse
[3], The results showed thatalum inum powder gave the
smallest affected heat and the highest M RR.Theeffects o f
electrical parameters onMaterial Removal Rate (M RR), Tool
W ear Rate (TW R) and surface roughness (SR) were
investigated in machining nickel alloy with aluminum pow der
mixed in dielectric fluid and reverse electrode polarity [4]. The
effect o f copperelectrode polarityon the quality o f SKD61 steel
surface after EDM with alum inum powder was mixed in
properties changed significantly and the special machined dielectric fluid was shown [5], SR has received optimal value
r. i i i i • 1 : '¡V iÄ j o i-ee* n ^ lo f ih r T lii» in fln p n r ’p r\ r ttap» n n n /n p r surface showsa white layer with more microcracks and low
toughness. The change o f the surface layer that reduces the
ability o f the working dies is necessary to improve the surface
quality o f the work product o f this type. In practice, the
machined surfaceby EDM often requiresfine machining, such
as grinding, polishing, etc. to rem ovelayer defect.
''V i *
The research results showed that, PM EDM is the effective
method to eliminate the limitations o f EDM. PM EDM can
improve the productivity and machining quality o f EDM.
However, the working principle o f PM EDM processis very
complex, so it is affected by many technological parameters.
Beside the influence o f the parameters, such as current, pulse
on time, pulse o f time, concentration o f powder, powder
materials, the electrode polarity alsohas significantimpact on
the quality o f the machined surface. The negative polarity of
copper(<l>l mm) electrode on SKD61 steel machining by EDM
with titanium powder mixed in dielectric fluid created the
coating hardness o f 2000 HV on the surface o f the workpeice
[1]. W hentungsten powder was mixed in dielectric fluid in
EDM with negative polarity copperelectrode also created a
surface layer o f the steel mould (OHNS, D2 and HI 3), which
increased the microhardnessby 2 times [2].'The negative
polarity o f tungsten (<t>l mm) electrode was used to evaluate
the influence ofaluminum and silicon powder on the thickness
Paper ID: SUB153385
with reverse electrode polarity. The influence o f the powder
Al, Cr, Cu, SiC on S K D ll steel surface in EDM with reverse
electrode polaritywas introduced [6]. The results showed that
Al powder gaveSR and thickness affected by the minimum
heat pulse with positive electrodeand then increased
respectively in thfe materials pow der Cr, SiC and Cu. The
positive electrode polarity o f copper was used to research the
effect o f Si powder to M RR in AIST D2 steel machining [7].
The results showed that current intensity and powder
concentration werethe two param eters having thegreatest
impact on MRR. The pow der Al, Cr and Al + Cr mixed in
dielectric fluid affected the surface quality o f steel SKD61
after EDM withCu reverse electrode polarity[8]. The powder
o f Al, Cr and Al + Cr increased the hardness and strength
erosion o f the SKD61 steel surface. The smaller particle size
leads to smaller surface roughness. The copper
electrodepolarityhave little effect on the TW R in EDM with
graphite powder mixed in dielectric fluid. The reverse
electrode polarity gavesm aller TW R [9]. The influence o f the
concentration and size o f Al pow der andelectrode polarityon
the MRR, WR and SR in m achining 718 stainless steel by
EDM was introduced [10]. The results showed that the reverse
polarity hadstrong influence on M RR and the negative polarity
hadgood impact on WR and SR. The influence o f the electrode
polarityon MRR, TW R in EDM , Dry-EDM and PMEDM was
investigated [11]. The results indicated that the diameter o f the
Volume 4 Issue 4, April 2015
www.ijsr.net 1802
Licensed Under Creative Commons Attribution CC BY